List Of Screen Stencil Options
Graded Boring / Stepped Layer Forming
Partially changing the thickness of a photo emulsion on the printing surface of a screen stencil (the surface contacting the printed product) makes printing which had previously been difficult possible.
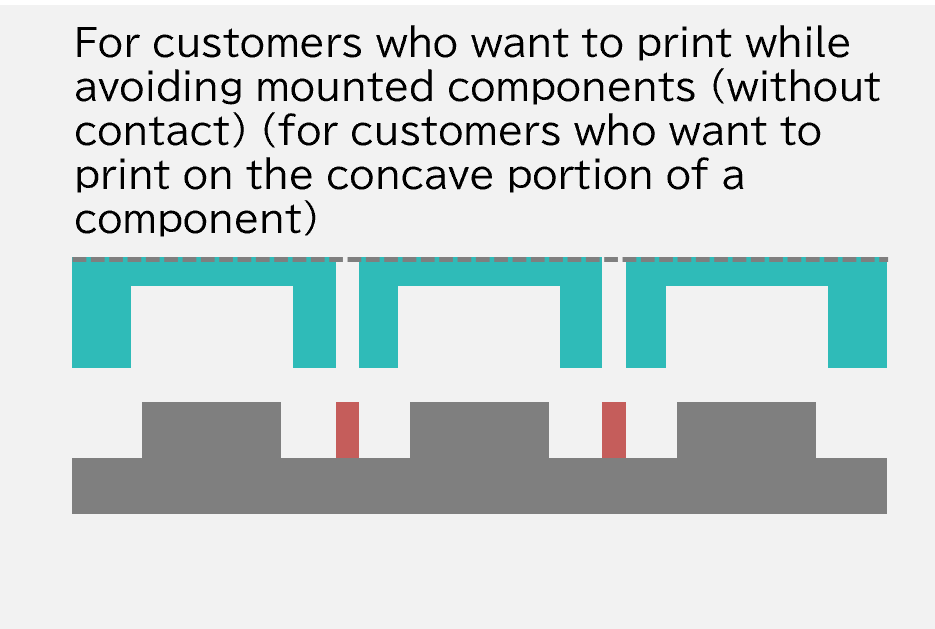
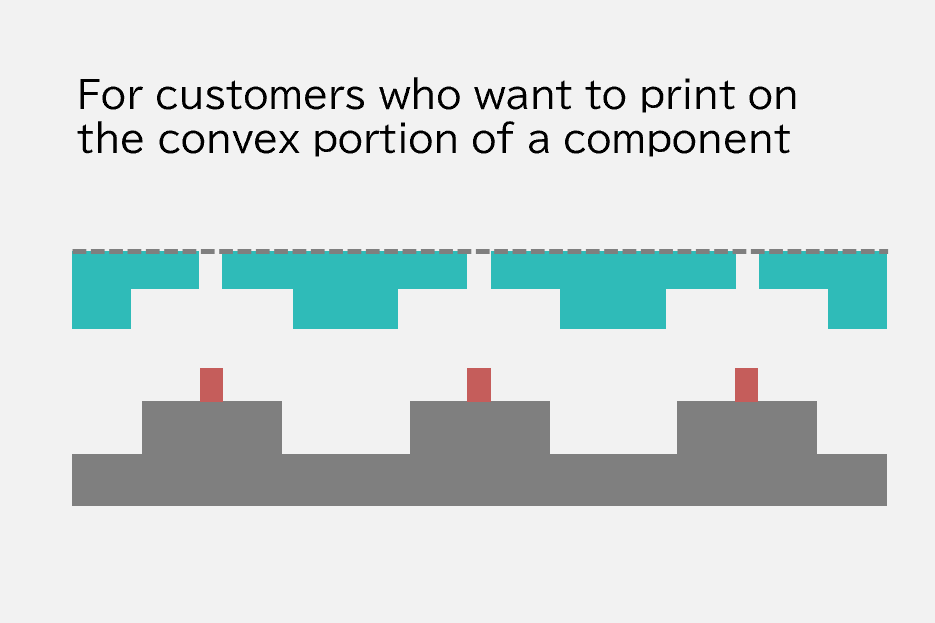
Special Processing – Water and Acid/Alkaline Resistance
This improves the water resistance of photo emulsion and capillary films. Additionally, resistance to acidic and alkaline inks and pastes is imparted.
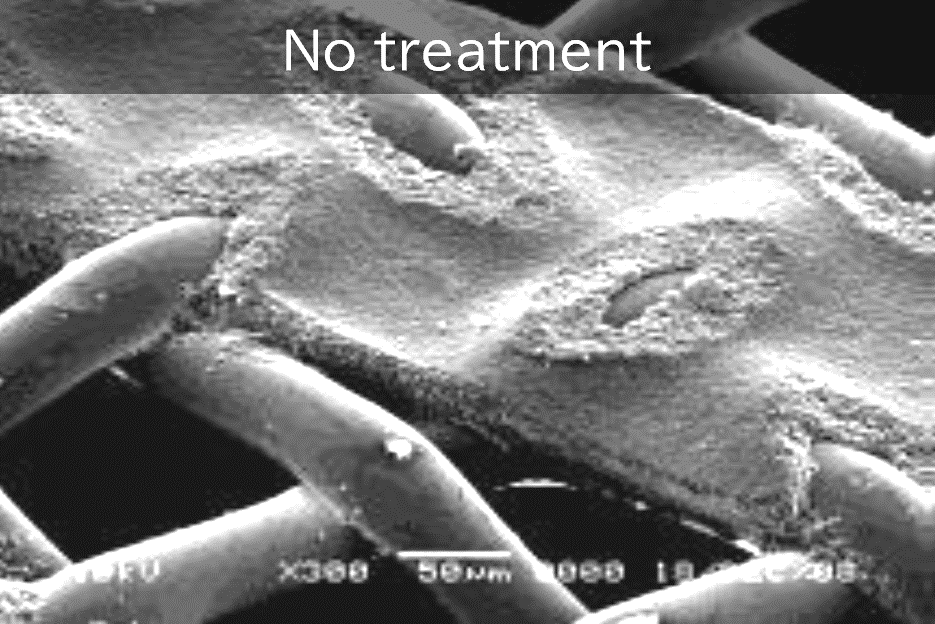
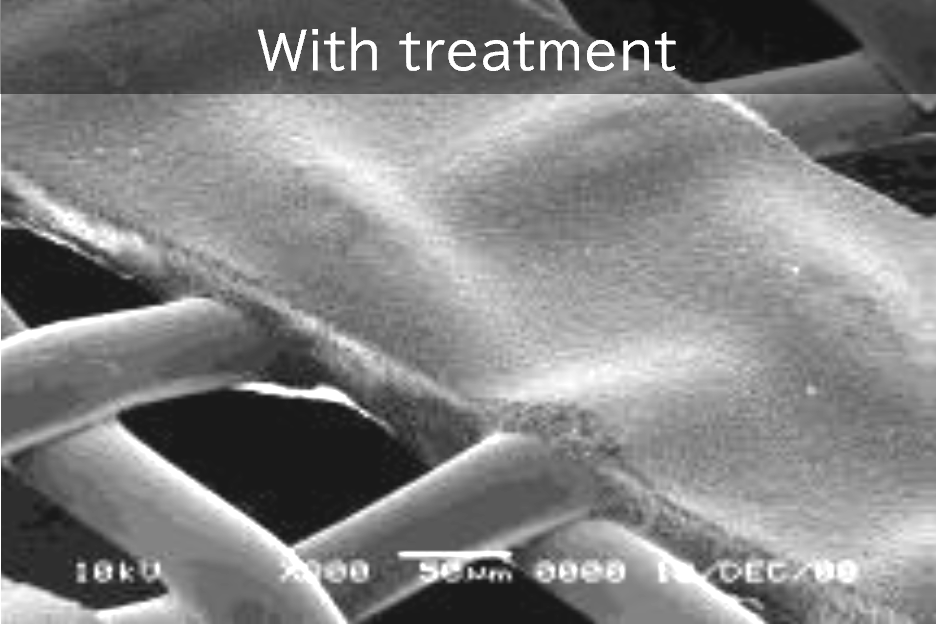
FT-SR/FT-SRP
Processing which imparts liquid repellency to photo emulsions and capillary films, and mesh. Inhibits bleeding (bleedthrough) of inks/pastes during printing.
Liquid repellency is maintained over a long period, even with repeated printing and/or stencil cleaning.
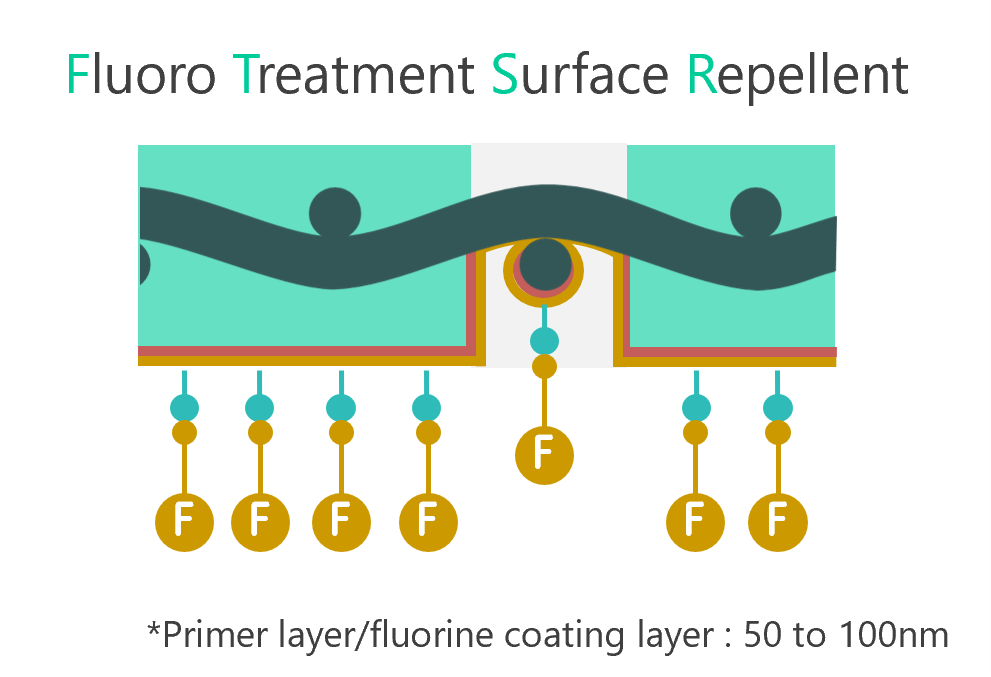
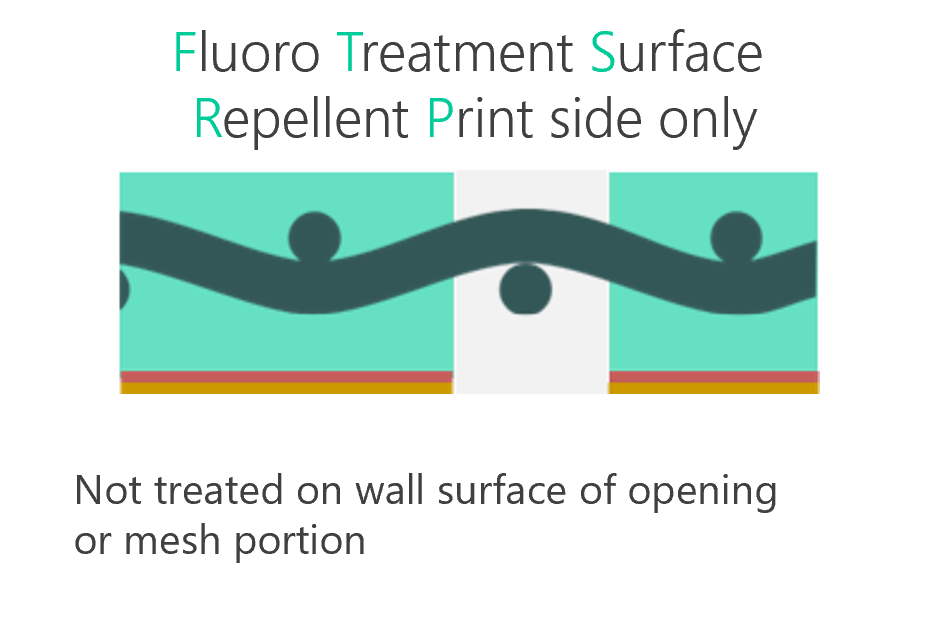
FT Processing
Processing which imparts liquid repellency to photo emulsions and capillary films, and mesh. Inhibits bleeding (bleedthrough) of inks/pastes during printing.
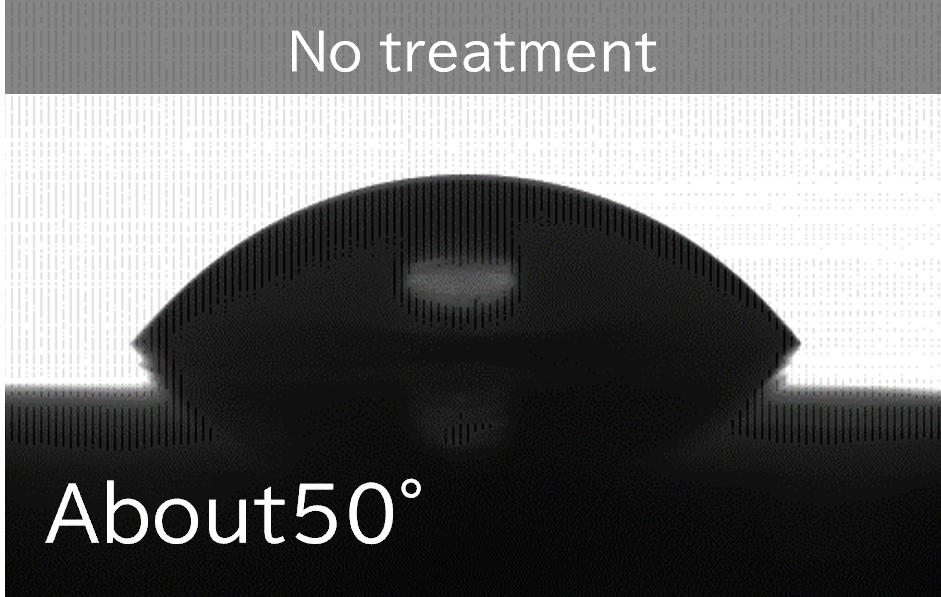
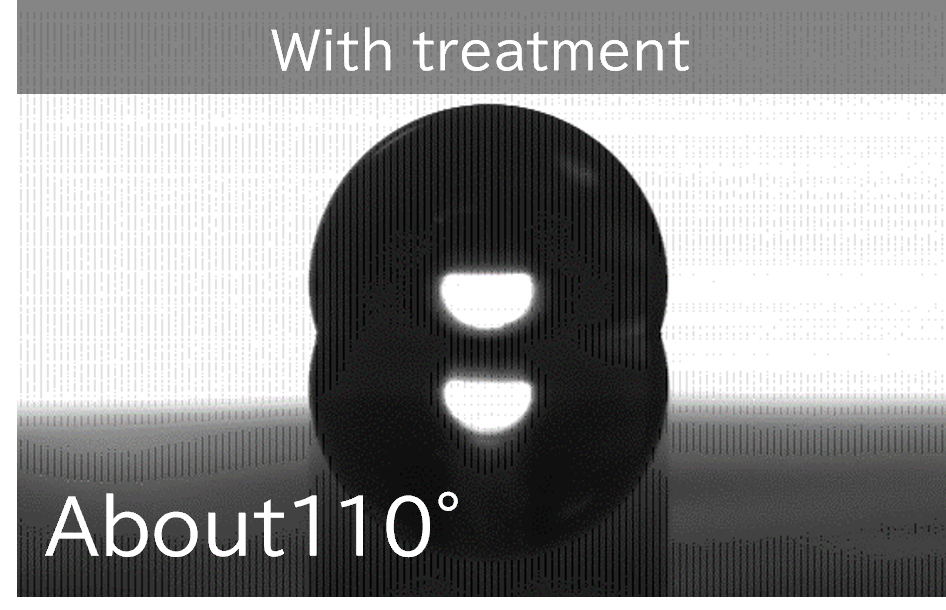
T Processing/TU Processing
Due to leveraging evenness in thickness and linearity, being benefits of the direct-indirect method, and creating irregularities on smooth surfaces to a degree, scratching which appears due to excessive adherence to the base material during printing is inhibited.
(Option only for capillary films)
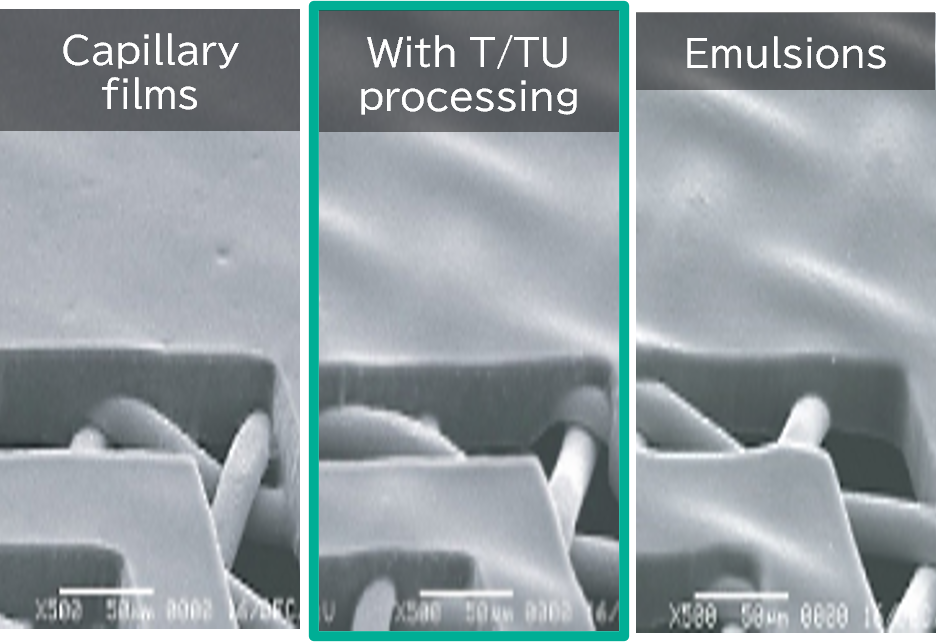
T-flat Processing
T-flat processing improves surface smoothness to the furthest extent possible. With a finish similar to that of a mirror surface, inhibits bleeding of inks/pastes during printing.
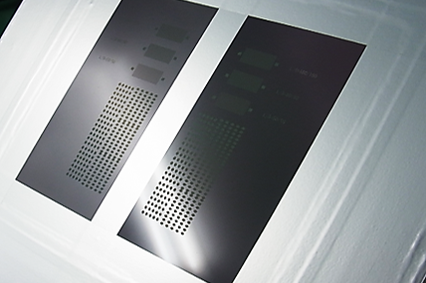
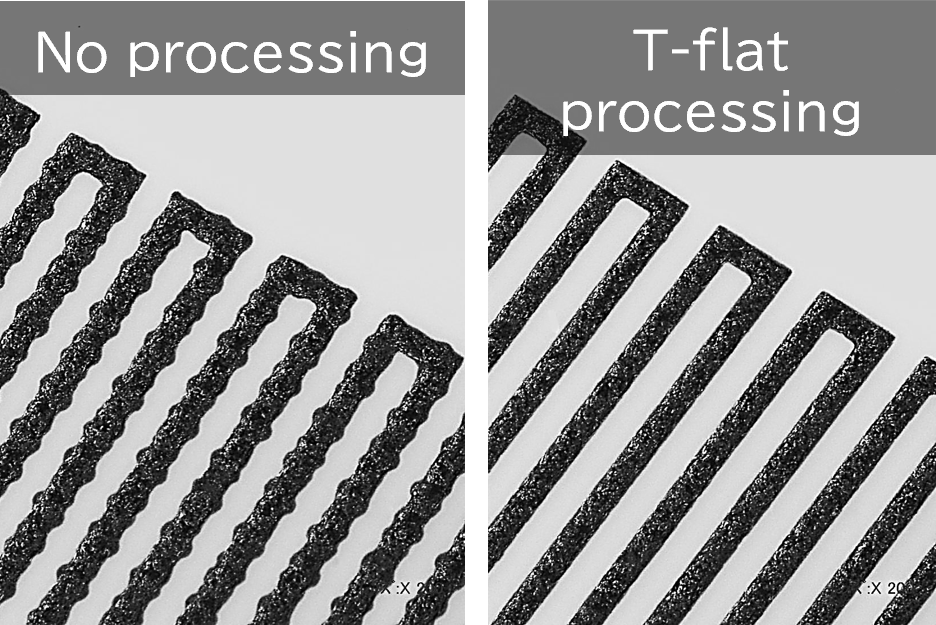
Flat Processing
Flat processing inhibits ink/paste bleeding during printing of a screen stencil in which emulsion thickness is thin.
(Option only for emulsions (liquid type))
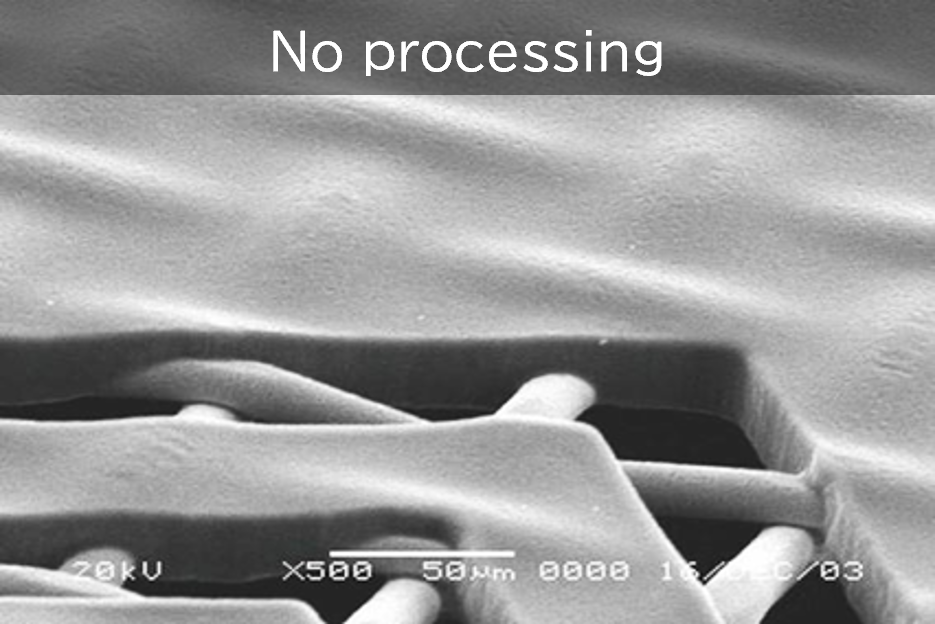
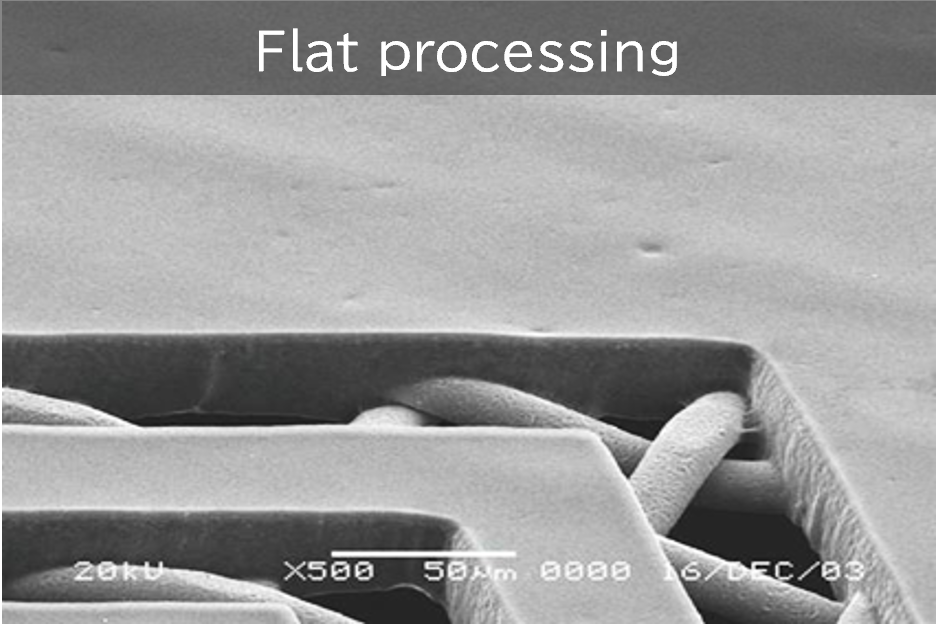
Bleed Inhibiting Photo Emulsion
Inhibits ink/paste bleeding (bleedthrough) during printing, facilitating screen stencil cleaning. Further, there are also types in which the photo emulsion itself has liquid repellency, whereby the liquid repellency effect can be maintained.
(Can only be selected as an option for screen stencils)
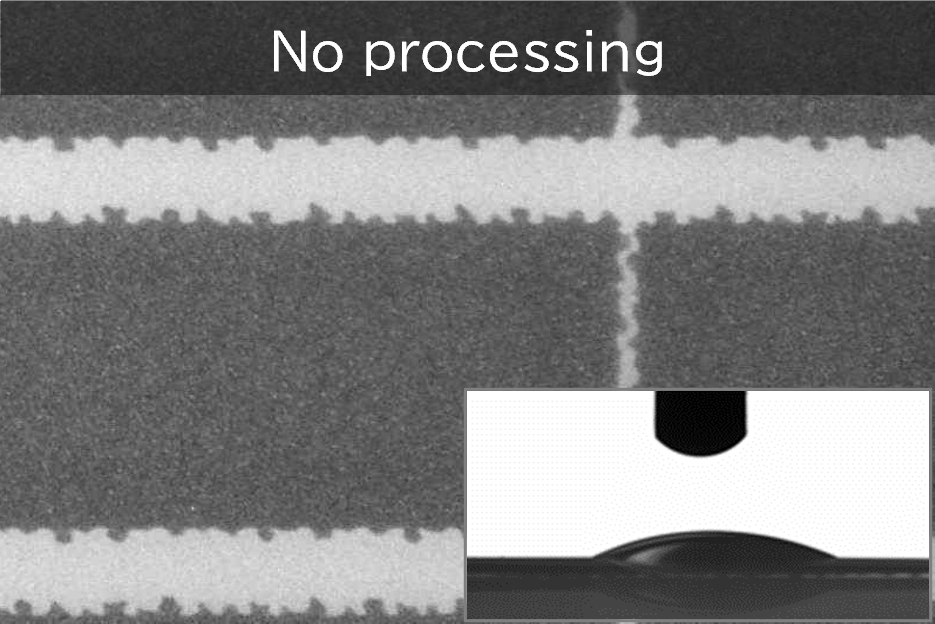
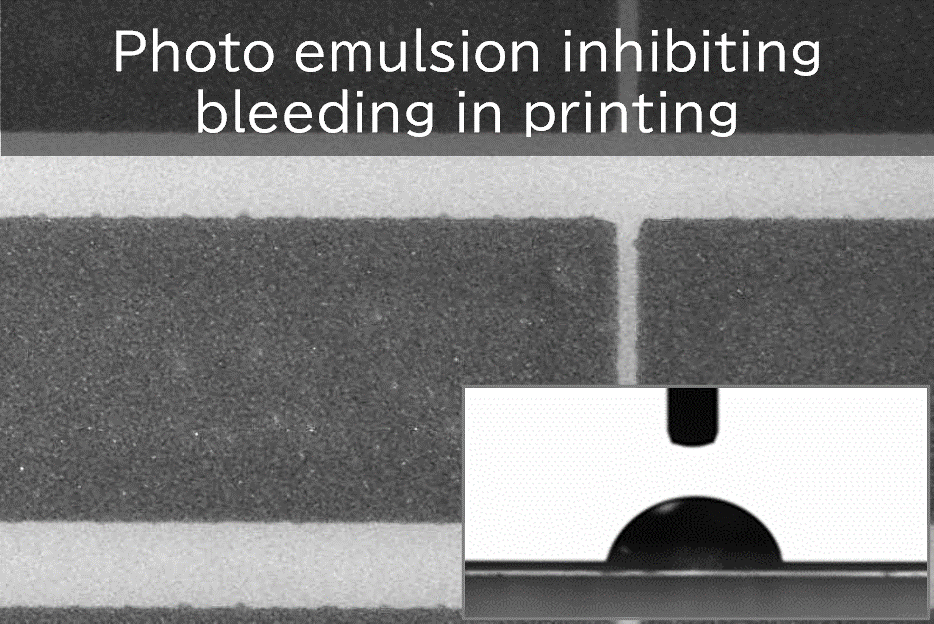
Next Generation Ultra-High Resolution Photo Emulsion
Photo emulsion which further improves upon the resolution of existing ultra-high resolution photo emulsion.
Fine lines as low as 15 µm can be mass-produced.
(Can only be selected as an option for screen stencils)
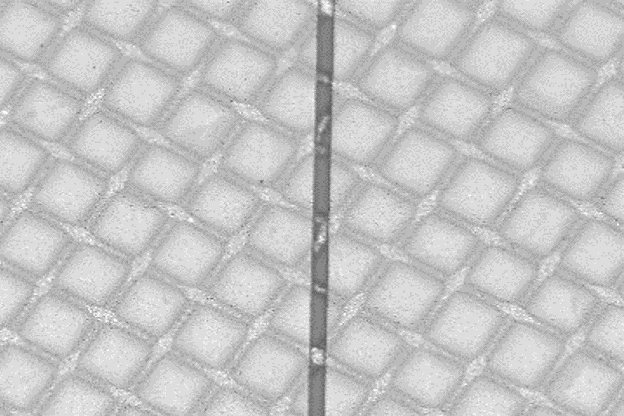
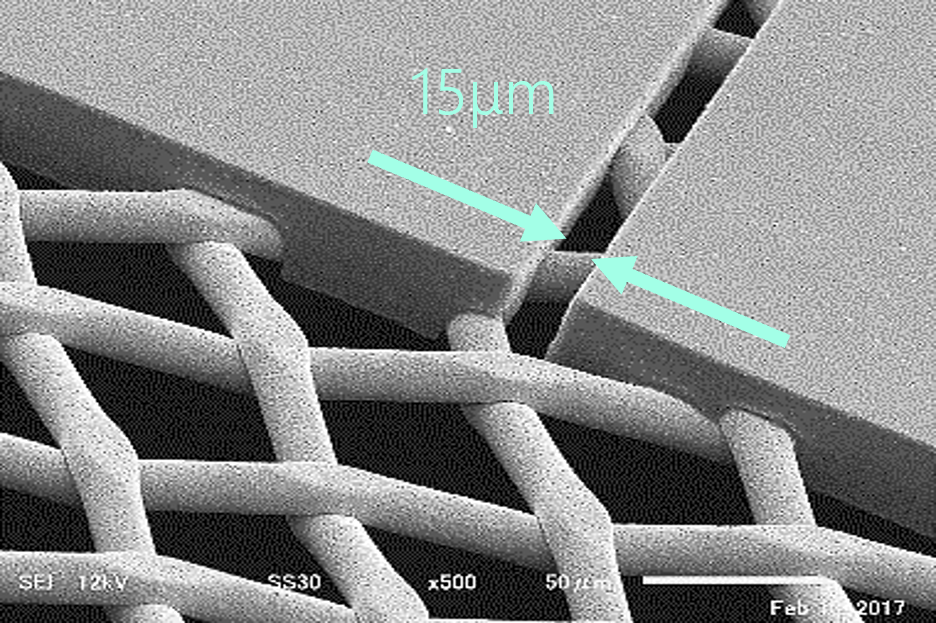
Ultra-High Resolution Photo Emulsion
Special photo emulsion achieving both ultra-high resolution and high solvent resistance; optimally suited for printing of fine lines.
(Can only be selected as an option for screen stencils)
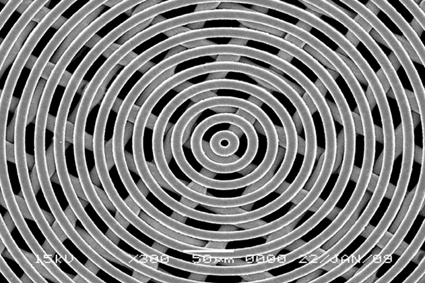
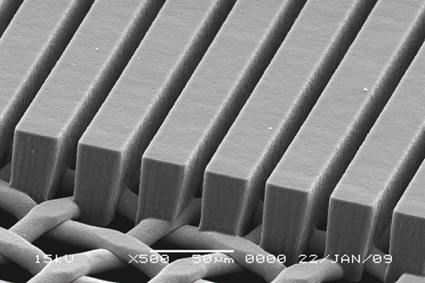
Polar Solvent Resistant Photo Emulsion
A dedicated emulsion with resistance to polar solvents such as NMP (N-methyl-pyrrolidone) and alcohols.
(Can only be selected as an option for screen stencils)
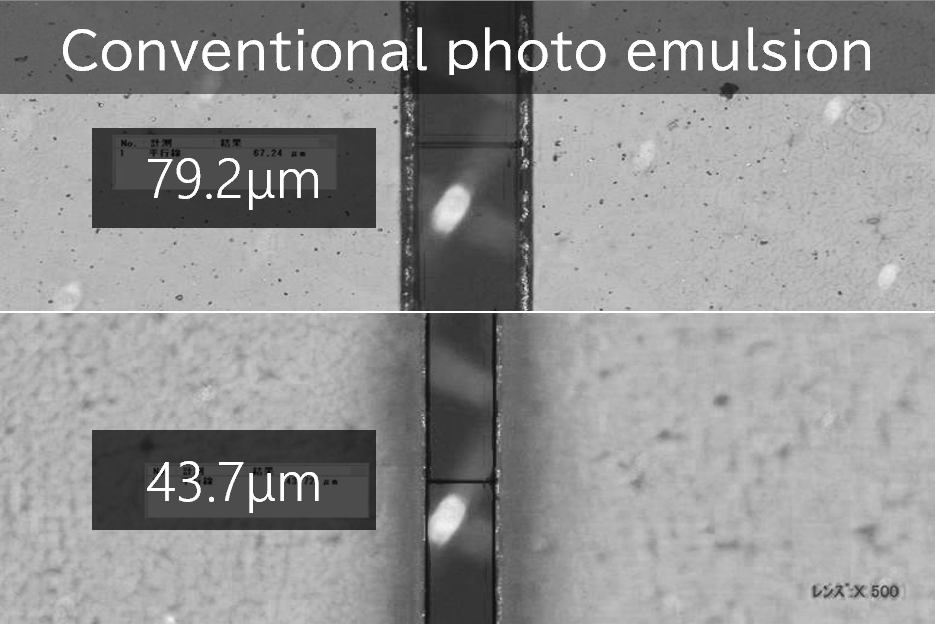
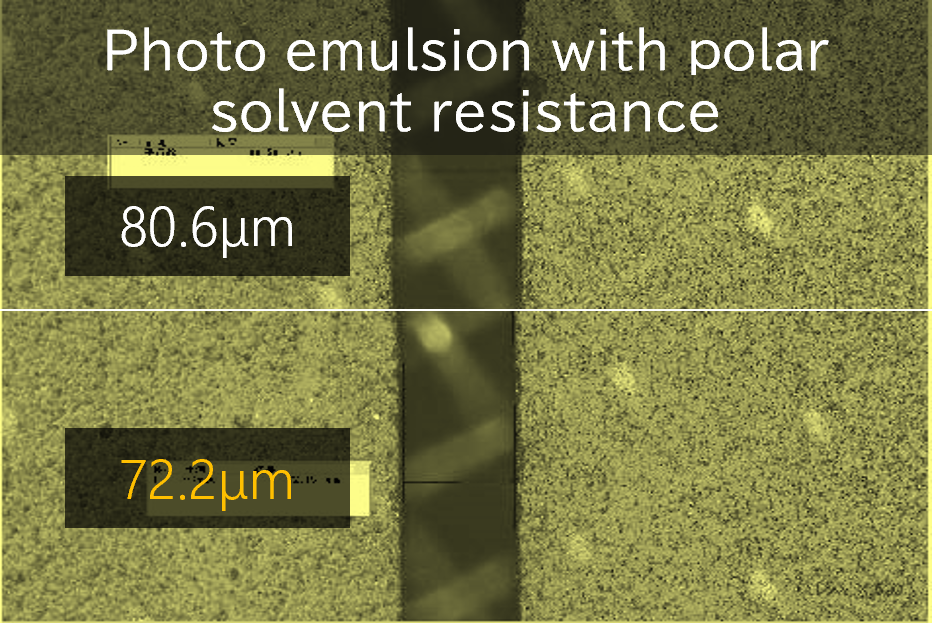
High-Resolution Capillary Films
A capillary film with high resolution, used only for screens made in our facility.
(Can only be selected as an option for screen stencils)
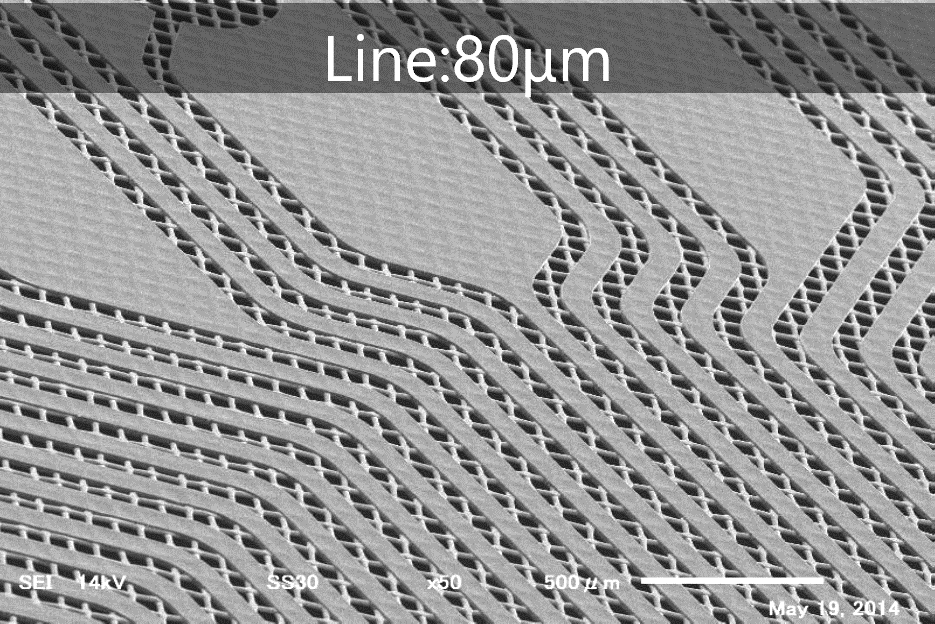
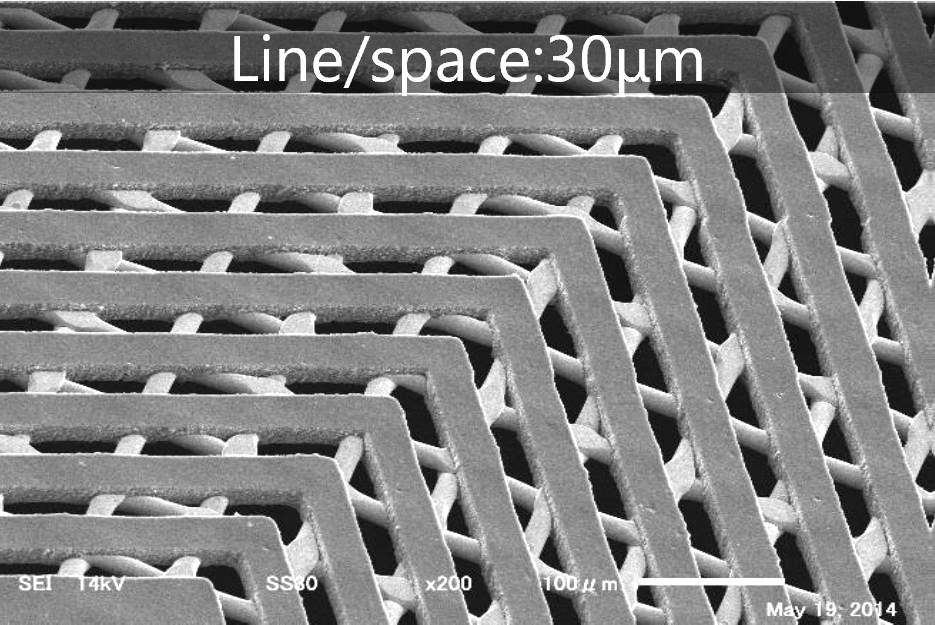
High-Resolution Emulsion
An emulsion with high resolution, used only for screens made in our facility.
(Can only be selected as an option for screen stencils)
Roller Treatment
By releasing residual stress due to the pseudo-printing load, great dimensional variation occurring at the initial stage of printing is inhibited. Positional precision is improved.
*Pseudo-printing: Since treatment is performed with a rigid urethane roller, there is no damage.
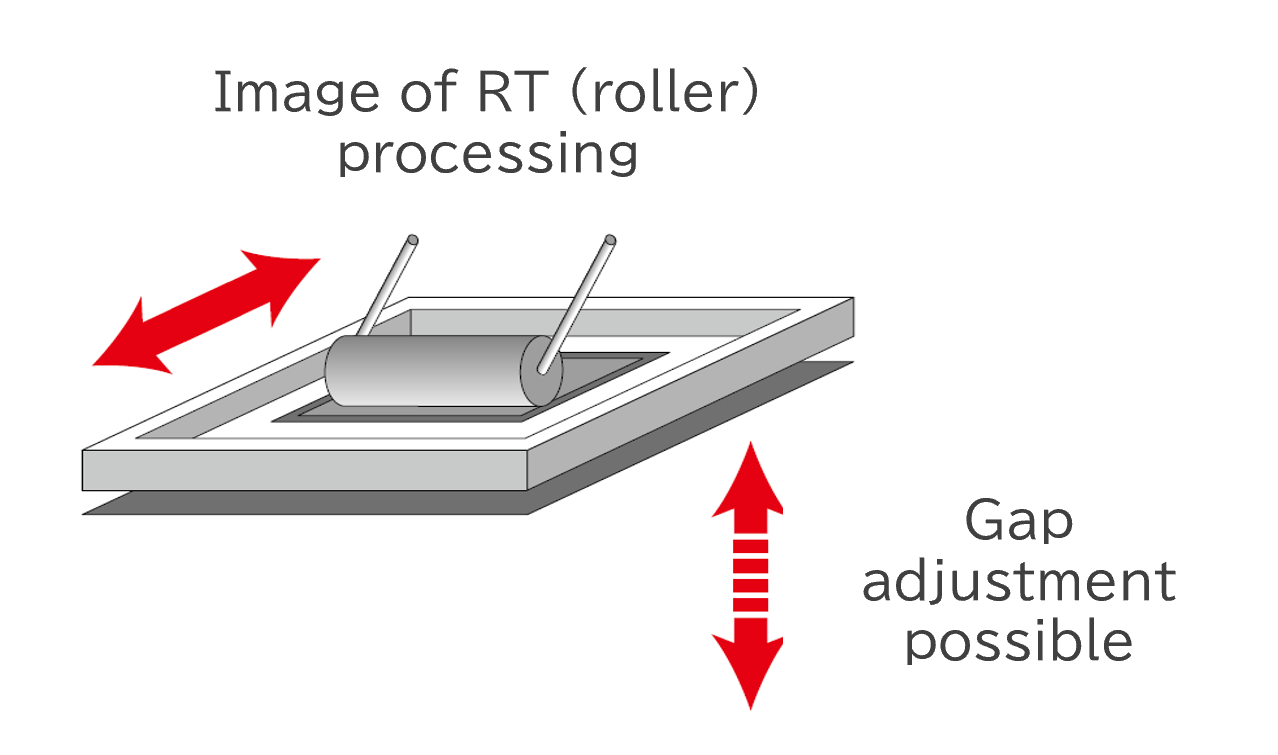
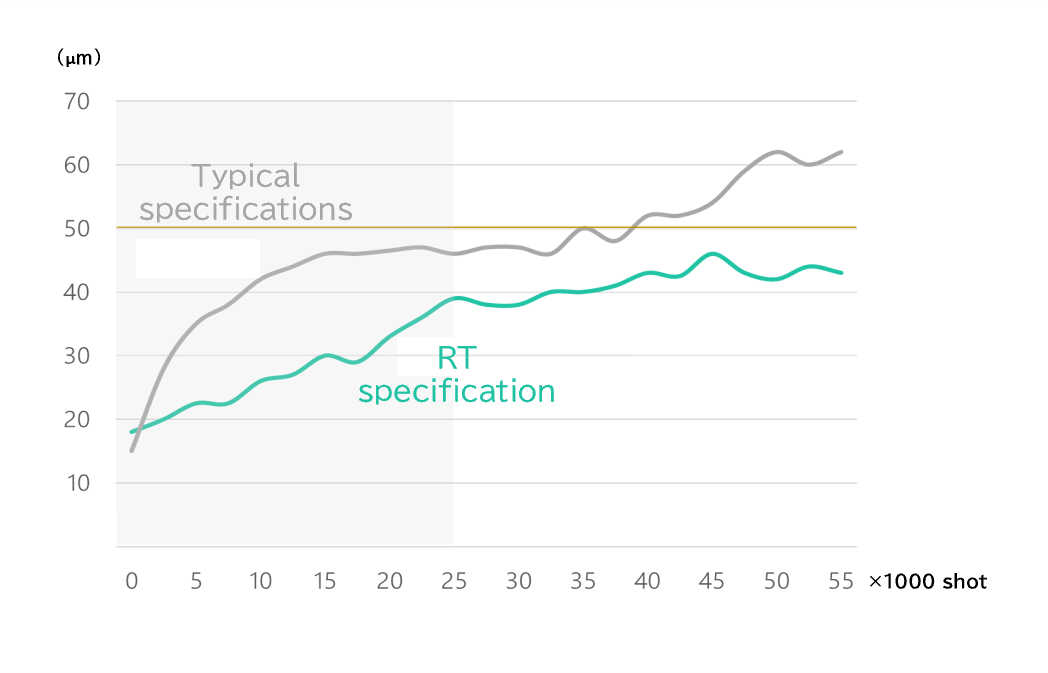
Strengthening of Outer Peripheral Portion
By reinforcing the outer peripheral portion (polyester mesh portion) of a combination screen stencil with metallic foil to increase rigidity, positional precision of the screen stencil can be improved and changes over time during printing can be inhibited.
This is effective in inhibiting dimensional variation in the early stages of printing and dimensional variation due to stress during printing.
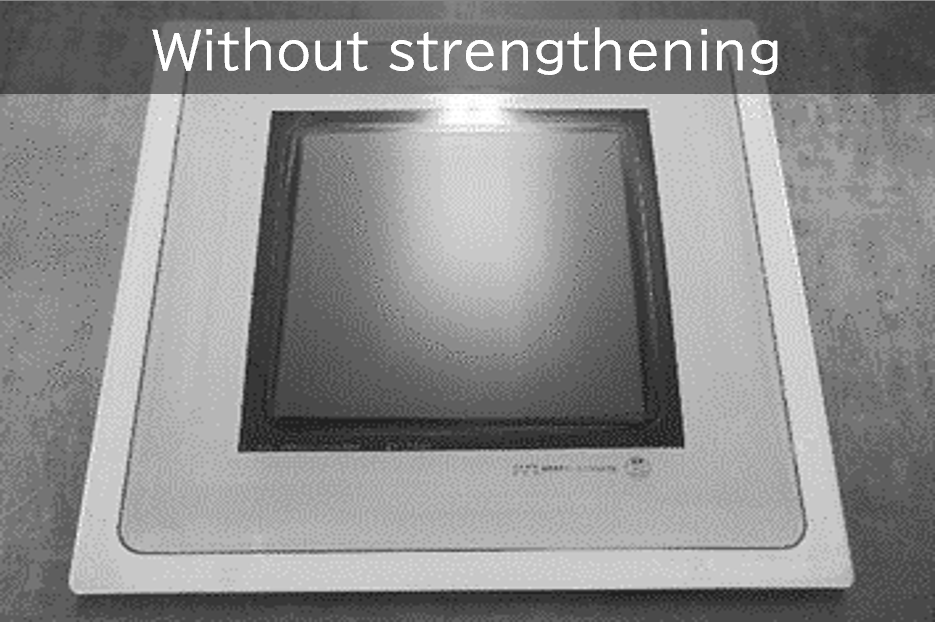
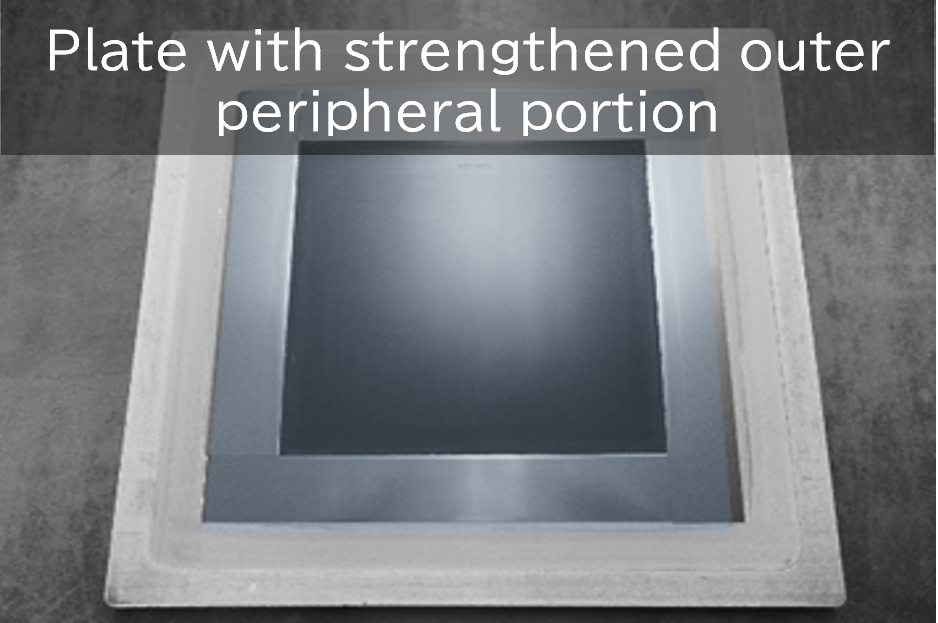
Blasting
Conducting blasting on mesh, being the supporting body of photo emulsion, makes it possible to expect improvement in resolution of screen making due to inhibition of halation during exposure, improvement in adhesiveness, and improvement in paste permeability due to improvement in paste wettability.
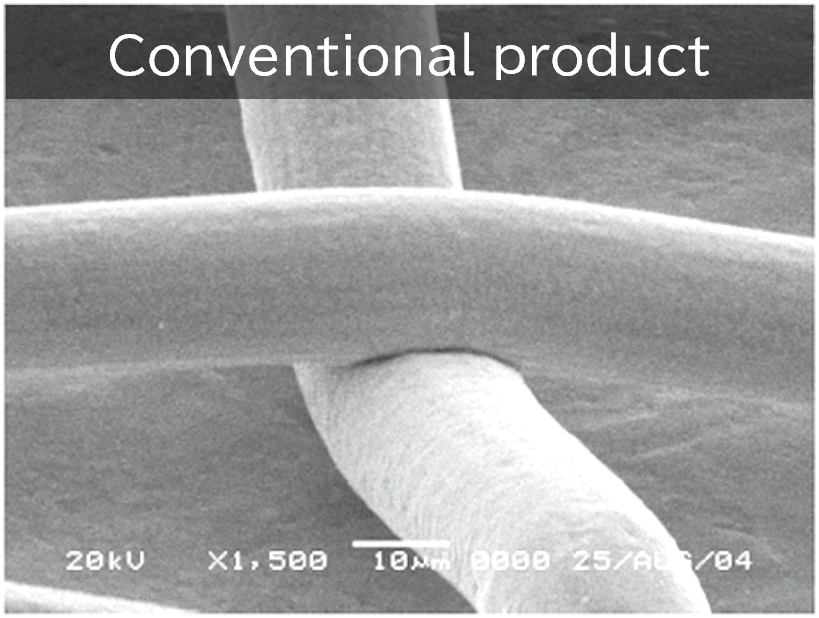
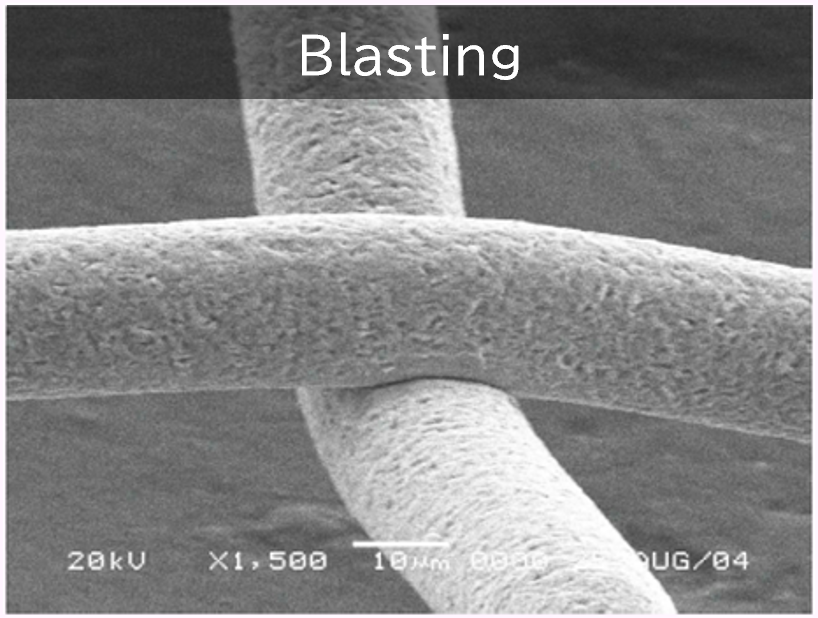
Combination
Compared to screens where stainless steel mesh is only used, printability is improved and deviation during printing is inhibited. Decrease in cost due to using less stainless steel mesh (expensive).
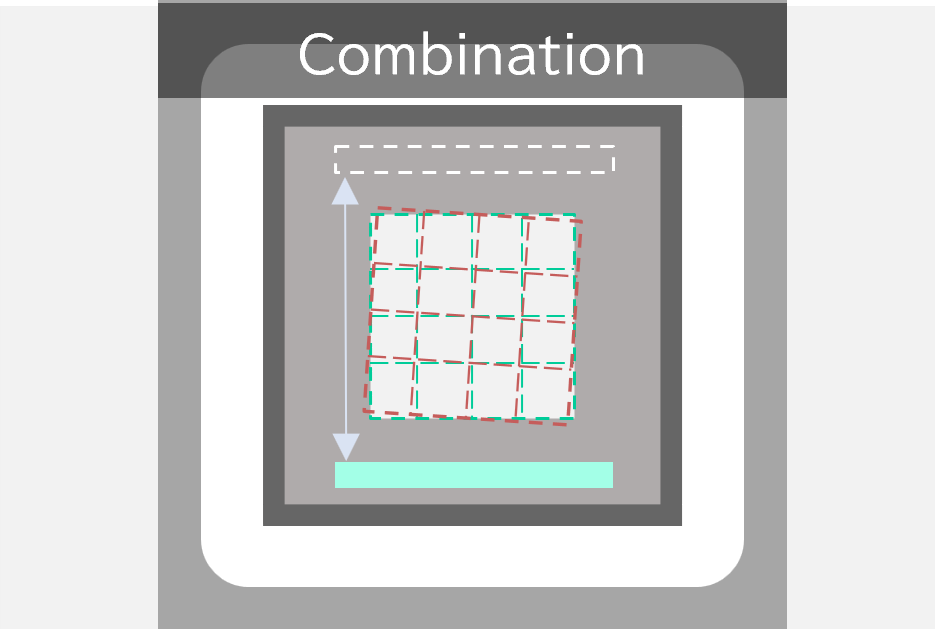
Metal Plating
By covering mesh with nickel plating to intersections, warping during printing is inhibited. Due to the maintenance/improvement of positional precision in printing, an increase in the number of printing shots and improvement in durability can be expected.
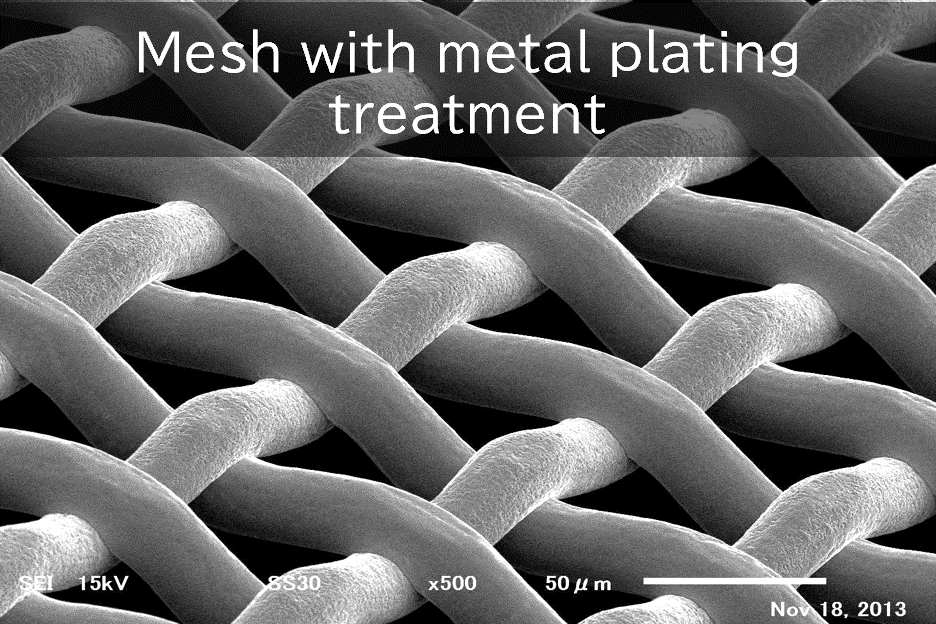
Calendering
Using a rolling apparatus, mesh thickness can be specified to units of 1 um. (Some limitations apply) By increasing treatment strength, the mesh becomes resistant to stretching, whereby positional precision in printing improves.
*By adding blasting, paste permeability toward the back side of the mesh intersection also improves.
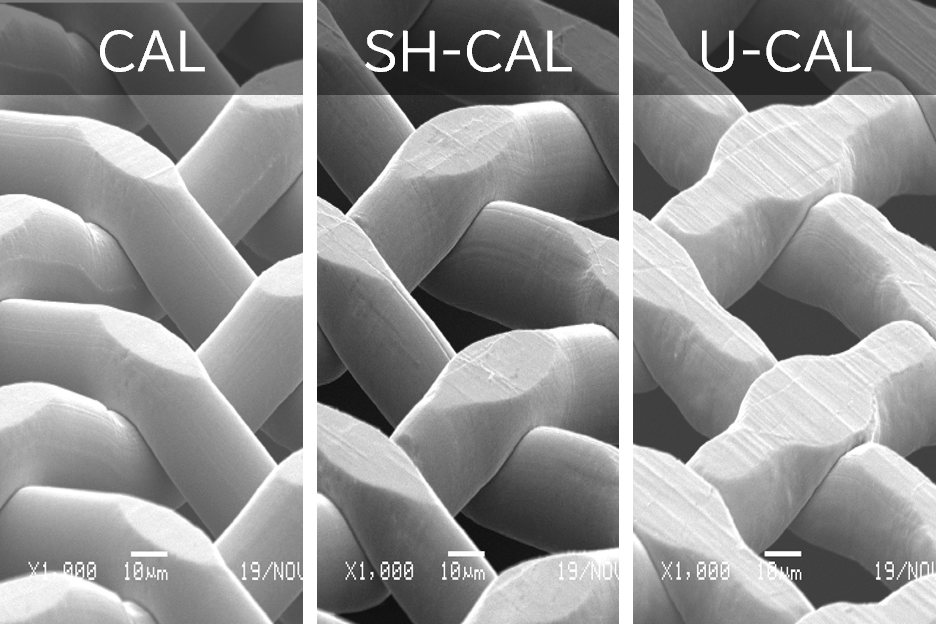
3D Mesh
3D mesh has a unique structure in which only one side of the threads are bent and treated, resulting in a mesh thickness is approximately three times that of the wire diameter.
Mesh intersections contacting with the product surface decreases, contributing to better leveling and evenness of printed film thickness.
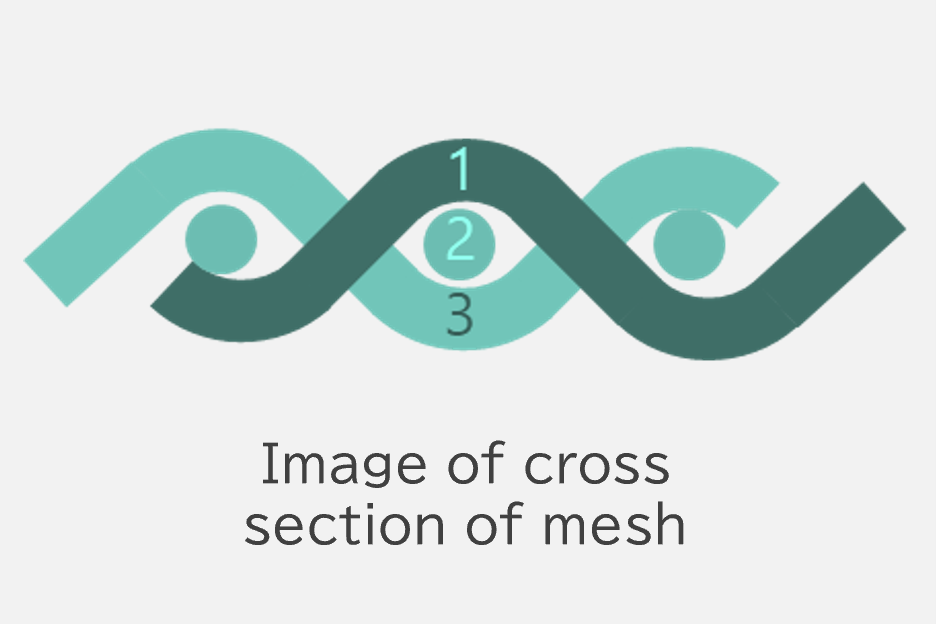
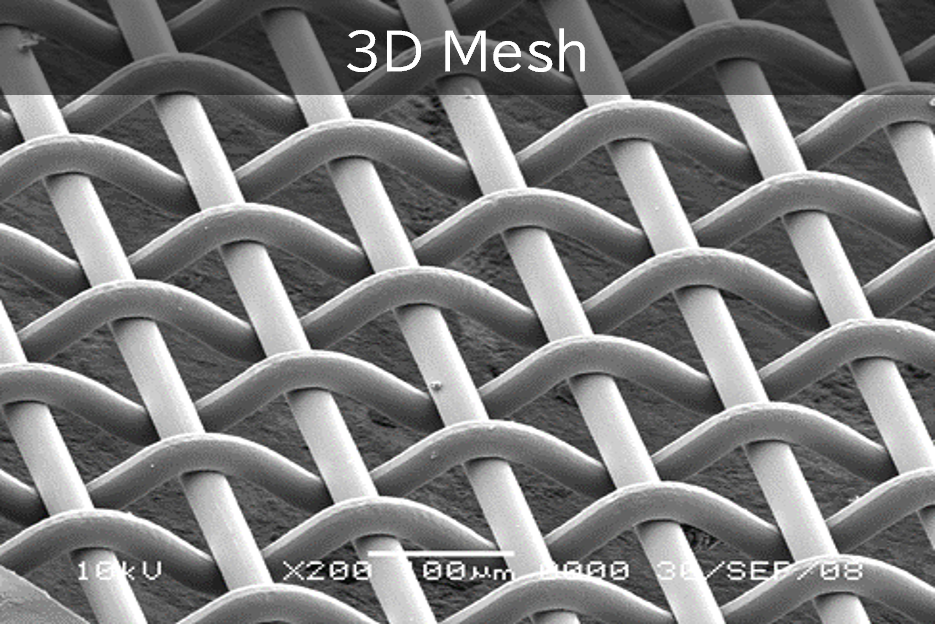
Black Mesh
By performing this process on the surface of stainless steel, diffused reflections during exposure are prevented, and emulsion wall surfaces are clearly resolved.
*Further, the effects are improved by performing this together with blasting.
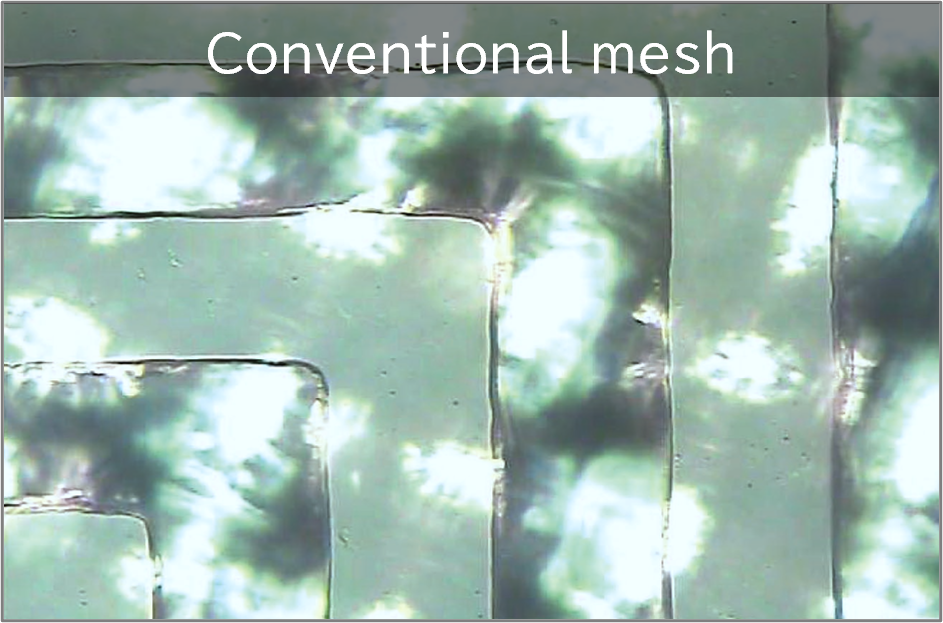
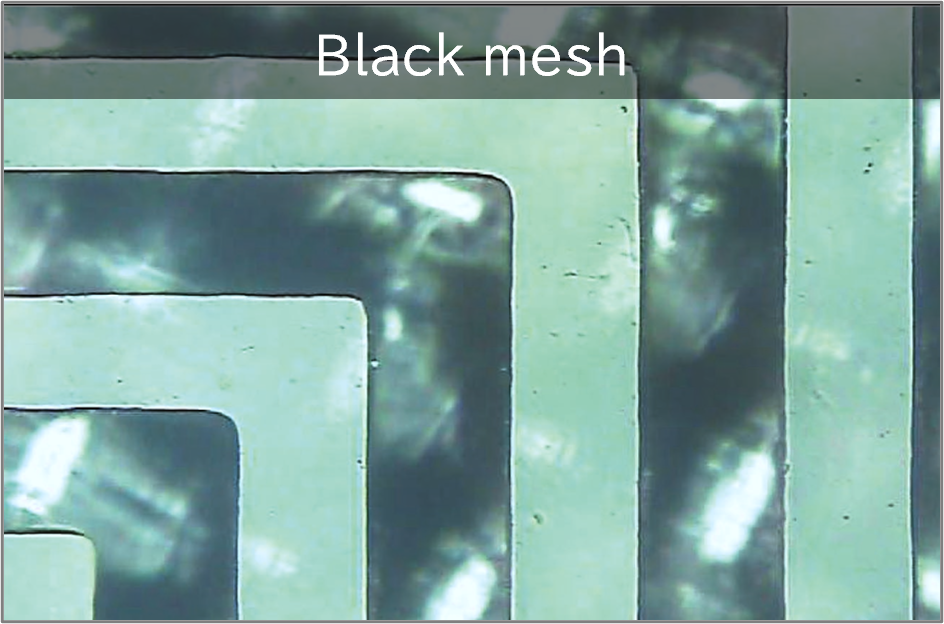
Tungsten Mesh
This mesh uses tungsten as its material.
It is more resistant to stretching than stainless steel mesh, having high strength.
High-Strength Stainless Steel Mesh
Compared to standard products, it uses materials having three times the strength, as well as low elongation. A mesh is made having a high opening percentage of 60%, which also increases the paste deposit amount.
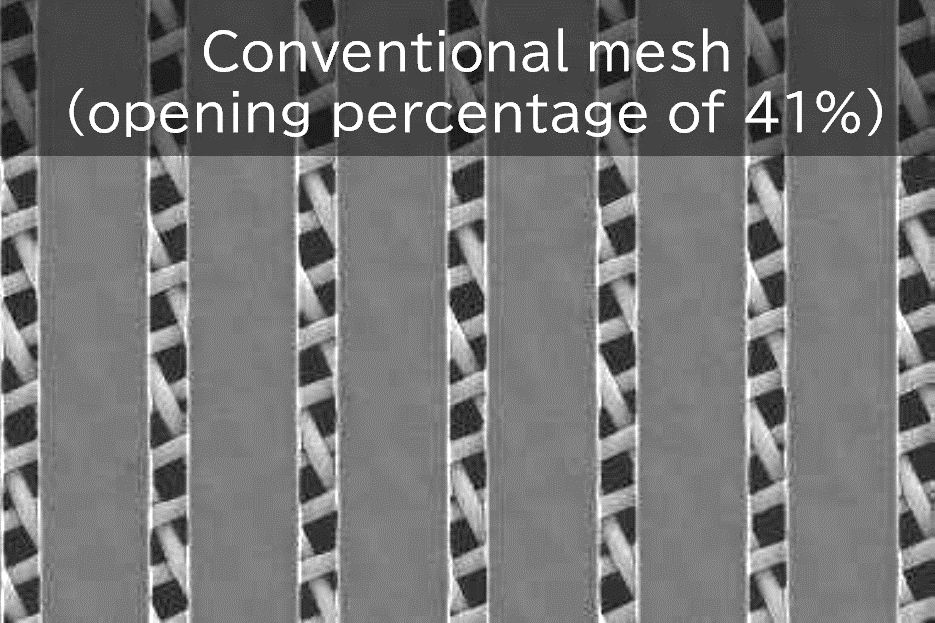
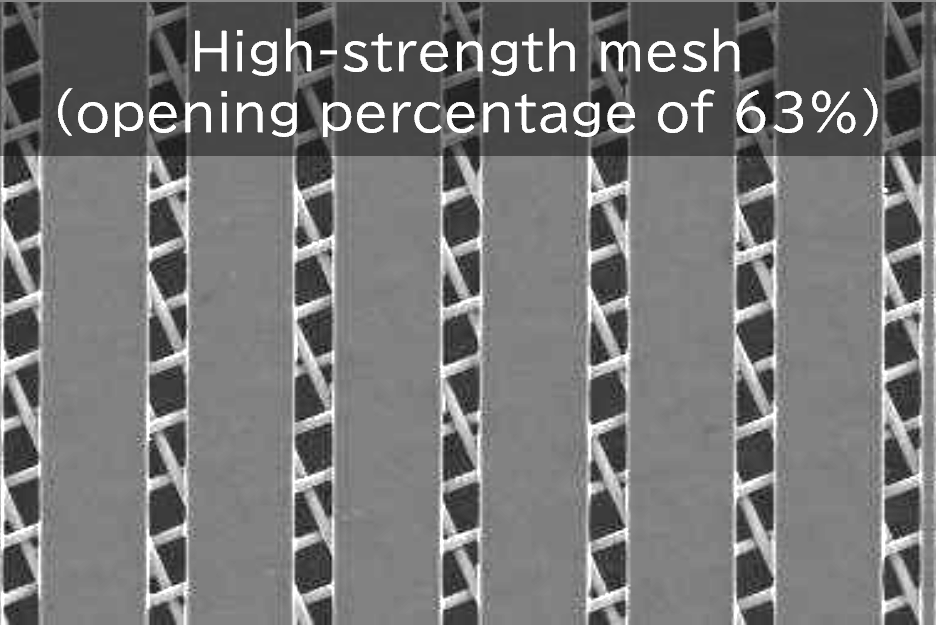